Quand la GMAO en place ne suffit plus…
Ce groupe agroalimentaire international a souhaité mettre en place des outils qui permettent l’analyse avancée de ses coûts de maintenance et qui facilitent les interactions entre production, maintenance et utilités.
La GMAO en place n’offrait ni l’évolutivité ni la connectivité requises. Avec son design vieillot, elle n’était en outre pas très appréciée des équipes de maintenance. Il a donc été décidé de la remplacer par WiW Maintain, la GMAO de The WiW.
La situation initiale de ce cas d’usage correspond à des problématiques partagées par de nombreux industriels : comment dépasser le « simple » suivi de la maintenance et optimiser la gestion des stocks de rechanges ? Comment construire et diffuser une vision opérationnelle commune ? Comment préparer la connexion des installations et intégrer automatiquement les données de production ?
Le contexte
Au commencement de ce projet, la situation était la suivante :
- une GMAO « classique », globalement peu (ou mal) utilisée
- absence de connexion entre la GMAO et le logiciel de gestion du magasin (module WMS de l’ERP en place)
- impression papier des bons de travail et ressaisie des comptes-rendus
- des calculs et des suivis annexes faits sur un tableur
- une faible pénétration générale des outils numériques, notamment mobiles.
Quelques chiffres :
- site de 200 personnes
- neuf lignes de production
- environ 400 machines
- équipe maintenance de 15 personnes
- près de 12 000 références de rechanges en magasin
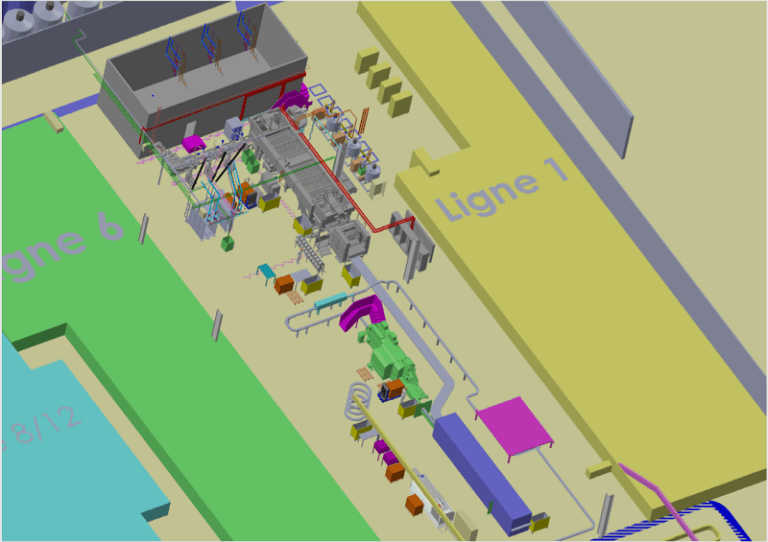
La problématique
Comme sur tous les sites de production, avoir une maintenance performante et efficiente est une priorité stratégique pour la direction. Parmi les enjeux :
- fiabiliser et assurer la disponibilité des lignes de production (dans ce cas client, un arrêt peut entraîner la mise au rebus de la production en cours s’il dure plus de quelques minutes)
- assurer la juste maintenance : ni trop, ni trop peu, au bon moment et au meilleur coût. La direction souhaite notamment introduire une méthodologie d’optimisation anglosaxonne en vigueur sur d’autres sites du groupe
- optimiser la gestion du stock de rechanges et réduire son coût, sans perte d’efficacité
- mettre à la disposition des équipes des outils qui simplifient leur travail et leur font gagner du temps
- fluidifier les interactions entre les équipes de production et celles de maintenance
- couvrir l’ensemble des besoins (préventif courant, correctif, amélioration et révision annuelle) avec les équipes en place
- faciliter le partage des connaissances entre les recrues et les équipes en place
- anticiper les prochaines évolutions technologiques : installations connectées, maintenance augmentée, IoT…
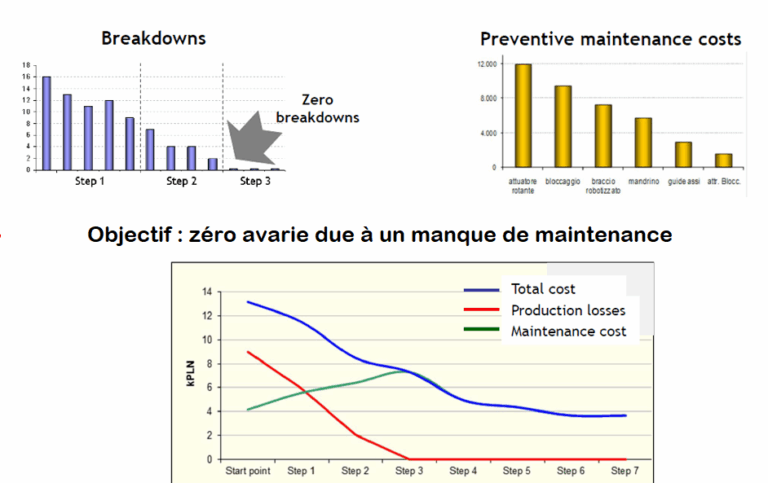
Le choix de la solution proposée par The WiW
The WiW a répondu au cahier des charges résultant de la prise en compte de cette problématique et des dimensions techniques, humaines et organisationnelles :
- avoir un outil unique, complet, évolutif et qui puisse être ouvert aux équipes de la production et des utilités
- proposer des interfaces simples et ergonomiques adaptées aussi bien au travail au bureau qu’à la consultation sur mobile
- mieux collecter et historiser les informations disponibles sans accroitre la charge de travail
- mettre en place des outils d’analyse et de reporting compatibles avec les standards propres au groupe
- pouvoir mobiliser l’ensemble des données à des fins d’analyse (faits techniques, retours d’expérience, optimisation des gammes…)
- calculer automatiquement les KPI (MTBF, TRS…) et les KAI (Key Activity Indicators)
- supprimer les impressions papiers, les comptes-rendus sur feuille, les ressaisies, etc.
- Préparer la connexion des équipements à la GMAO pour intégrer automatiquement les compteurs, les alarmes, les consommations, etc.
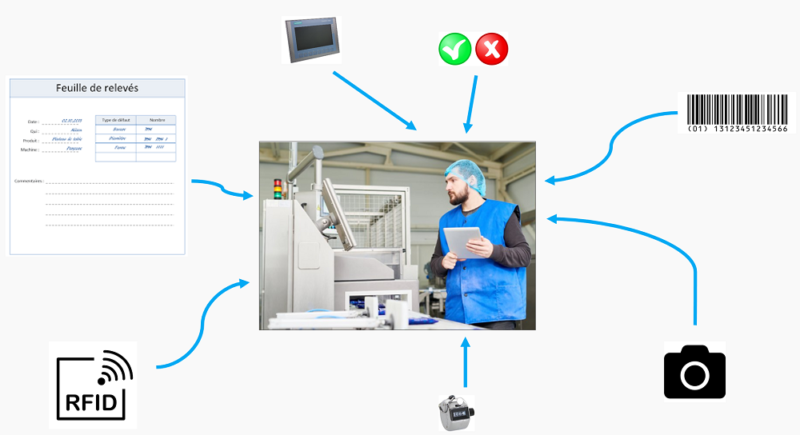
Le déploiement de la solution
WiW Maintain a été configurée pour prendre en compte les besoins spécifiques du site, notamment l’interaction avec WMS.
Une étape de préfiguration a tout d’abord permis de :
- définir la structure de données. Cette analyse initiale pose les bases sur lesquelles bâtir les outils d’analyse tout en permettant d’intégrer les données de l’ancienne GMAO
- définir avec les utilisateurs les futures interfaces
- tester in situ le matériel à utiliser par la suite : smartphone ? tablette légère ou durcie ? PC portable ?
Dans un deuxième temps, les tâches suivantes ont été réalisées :
- création automatisée de l’ensemble des installations (400 machines, 6200 ensembles et sous-ensembles, 8800 pièces élémentaires…)
- création, pour une ligne pilote, des nouvelles gammes de maintenance
- mise en place d’un système d’identification des pièces par QR codes compatibles avec l’existant
- mise en place des premiers outils de pilotage du stock de rechanges
- coaching individualisé des techniciens « pilotes » pour affiner les interfaces et assurer une montée en compétence rapide.
Témoignage de Mathieu A.
Chef du service maintenance.
« L’usine a engagé depuis 18 mois un important processus de transformation numérique. De manière générale, nous voulons être plus efficaces, plus réactifs. De significatives réductions de coût, de délais, de non-qualité sont attendues. Pour cela, nous poursuivons plusieurs axes stratégiques à travers tout le site, dont la mise en place d’une GMAO puissante, simple d’utilisation et connectable aux autres systèmes de l’usine.
Avec WiW Maintain, The WiW a su proposer une solution de maintenance moderne et évolutive, dont le design a tout de suite plu aux équipes.
En outre, l’équipe de The WiW nous accompagne très efficacement à chaque étape du projet : visites régulières sur site, interlocuteur dédié, groupes de travail, coaching adapté à chaque utilisateur… nous sommes aidés, guidés et préparés pour chaque marche que nous franchissons. C’est très important pour l’acceptation de la démarche et le succès du projet.
Après la reprise de l’existant et l’absorption d’outils annexes, nous disposons à présent d’une base solide, exhaustive et fiable. Un premier ensemble d’outils est opérationnel et chaque mise à jour apporte de nouvelles fonctionnalités.
Le déploiement de WiW Maintain va se poursuivre dans les mois qui viennent pour couvrir l’ensemble des aspects techniques de l’usine et renforcer l’efficacité globale de toutes les parties prenantes des opérations : maintenance, production, utilités ».
